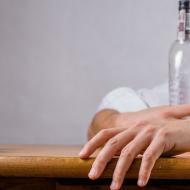
Syntetyczne supertwarde materiały i powłoki. Stopy supertwarde i materiały ceramiczne Właściwości składu materiałów supertwardych
Diamenty charakteryzują się dużą twardością i dobrą przewodnością cieplną (A = 137,9... 146,3 W/(m·K)). Odporność cieplna diamentów nie jest wystarczająco wysoka; Diamenty zaczynają grafitować w temperaturach 800...900°C. Regularny azotek boru CBN ma niższą twardość w porównaniu do diamentu, a przewodność cieplna jest około trzykrotnie niższa (λ = 41,86 W/(m·K)). CBN ma znacznie wyższą odporność na ciepło. Przekształcenie struktury sześciennego azotku boru w grafitową modyfikację sześciokątną rozpoczyna się w temperaturach 1200...1400°C i gwałtownie wzrasta po podgrzaniu do
1600...1800°C.
Materiały kompozytowe(polikryształy) otrzymuje się różnymi sposobami. I tak, polikryształy diamentu typu ballas (ASB) i carbonado (ASPC) otrzymuje się poprzez impregnację porowatych wyprasek powstałych z proszków diamentowych powłokami metalowymi. Stosując podobną technologię, materiały CBN-R produkowane są z sześciennego azotku boru. Do produkcji ostrzowych narzędzi skrawających, takich jak noże, opracowano materiały kompozytowe, takie jak PTNB, z mieszanin regularnego i wurcytowego azotku boru.
Diamenty syntetyczne produkowane są z materiałów węglowo-grafitowych w specjalnych komorach wysokociśnieniowych wykonanych z materiałów o dużej wytrzymałości. Wysoką temperaturę uzyskuje się poprzez przepuszczanie prądu elektrycznego przez urządzenie grzewcze.
Zacieniony obszar 1 odpowiada rzeczywistym warunkom przemiany grafitu w diament w obecności dodatków katalitycznych. Kreskowany pasek 2 pokazuje granicę bezpośredniego przejścia fazowego grafitu w diament.
W warunkach statycznych, stosując katalizatory, można otrzymać sześcienną siatkę diamentową z warstwowej sieci krystalicznej grafitu w warunkach wysokich ciśnień i temperatur (p = 5000...7000 MPa, T - nie mniej niż 1400...1500 K.). Katalizatory to metale, które w procesie syntezy występują w stanie ciekłym i są zdolne do rozpuszczania węgla w postaci cząstek o warstwowej strukturze grafitu. Z tych cząstek powstają jądra nowej fazy diamentowej.
Ryż. 16. Schemat fazowy
Węgiel „ciśnienie-temperatura”
Przemysł produkuje różnorodne proszki diamentów syntetycznych i naturalnych, stosowanych w różnych dziedzinach techniki.
Proszki diamentowe dzieli się w zależności od metody produkcji i wielkości ziaren na następujące grupy:
1. Proszki diamentowe do szlifowania Proszki diamentowe syntetyczne o wielkości ziaren od 40...50 mikronów do 630...800 mikronów produkowane są w głównych gatunkach: AC2, AC4, AC6, AC 15, AC20, AC32, AC50. Im wyższa liczba po indeksach AC, tym większa wytrzymałość ziaren diamentu.
2. Proszki diamentowe do szlifowania z powłokami powierzchniowymi ziaren.
Zastosowanie powłok z ziaren diamentu zwiększa trwałość narzędzi i zmniejsza zużycie diamentu. Standardowo stosowane są następujące rodzaje posypek ziaren:
Powłoka typu K z powłoką z węglika metalu;
Powłoka typu KM z powłokami ze stopów zawierających krzem;
powłoka typu NT, która jest węglikowo-metaliczna;
Powłoka typu A, w której zespół agregatów kilku ziaren diamentu posiada warstwę węglika metalu;
Powłoka typu AN jest modyfikacją powłoki A, charakteryzującą się wprowadzeniem dodatkowego napełniacza (węglika boru, węglika tytanu, elektrokorundu itp.) do agregatów ziaren diamentu.
3. Mikroproszki diamentowe o wielkości ziaren od< 1,0 мкм до 40.. .60 мкм.
Dostępne są w dwóch odmianach:
650.. Mikroproszki diamentowe w gatunkach AM z diamentów naturalnych i ASM z diamentów syntetycznych;
651.. Mikroproszki diamentowe gatunków AN z diamentów naturalnych i gatunków ASN z diamentów syntetycznych. Mają wyższą zdolność ścierną (25...30%) w porównaniu do mikroproszków AM i ASM.
Mikroproszki AM i ASM stosowane są do prac wykończeniowych wyrobów ze stali hartowanych, szkła, ceramiki itp. Do obróbki wyrobów z materiałów twardszych (korund, ceramika, diamenty naturalne i inne materiały trudnoskrawalne) mikroproszki AN i ASN są zalecane.
Mikroproszki stosowane są do produkcji narzędzi ściernych, a także do stosowania w postaci wolnej, nieutrwalonej w pastach i zawiesinach.
Przemysł produkuje mikroproszki o wielkości ziaren 60/40, 40/28, 28/20, 20/14, 14/10, 10/7 itd. do 1/0 mikrona. W oznaczeniu marek licznik pokazuje maksimum, a mianownik minimalną wielkość głównej frakcji proszku w mikrometrach.
1.2 Pytania zabezpieczające:
- Jaka jest struktura makrocząsteczek, które mają polimery?
- Jak zmienia się struktura oligomerów (żywic) podczas procesu utwardzania?
- Jakie oddziaływania międzycząsteczkowe zachodzą pomiędzy makrocząsteczkami?
- Jaką strukturę supramolekularną mają kauczuki w wysoce elastycznym stanie fizycznym?
- Co oznacza konfiguracja cis makrocząsteczek gumy?
- Jaką strukturę mają materiały grafitowe?
- Jaką strukturę mają szkła krzemianowe?
- Które przemysłowe tlenki szkła powodują powstawanie szkła?
- Jakie stany fizyczne ma szkło nieorganiczne w różnych temperaturach?
- W jakim stanie fizycznym formowane są produkty ze szkła krzemianowego?
- Jaką strukturę mają materiały szklano-krystaliczne?
- Jakie katalizatory stosuje się w produkcji materiałów szklano-krystalicznych?
- W jakim celu przy wytwarzaniu materiałów szklano-krystalicznych stosuje się dwustopniową obróbkę cieplną szkła?
- Jakie związki chemiczne stosuje się jako środki ścierne?
- Jakie są wymagania dotyczące materiałów ściernych?
- Z jakich dwóch elementów składają się narzędzia ścierne?
- Co oznacza budowa narzędzia ściernego?
- Jakie materiały należą do klasy materiałów supertwardych?
- Na jakie rodzaje materiałów supertwardych dzielimy się?
- Jakie właściwości mają diamenty i sześcienny azotek boru?
- Co to są materiały kompozytowe?
2 Lekcja praktyczna nr 2 „Wyznaczanie parametrów szlifowania materiałów niemetalicznych” (ME-3 Szlifowanie materiałów niemetalicznych)
Zadania na lekcję praktyczną
Podczas zajęć praktycznych student prezentuje prezentację (przekaz) przygotowaną w ramach pracy samodzielnej i badawczej. Prezentacja powinna zawierać: możliwości technologiczne tego rodzaju obróbki, ograniczenia, wyposażenie, osprzęt i narzędzia skrawające, kryteria wyboru COTS, możliwe sposoby automatyzacji.
Krótka informacja z teorii
Ogólna koncepcja szlifowania
W prymitywnych przypadkach użyj twardego, ziarnistego piasku lub twardszego szmergla, wylej go na twardą powierzchnię i pocieraj o niego obrabiany przedmiot. Ziarna kątowe toczące się pomiędzy obiema powierzchniami powodują dużą liczbę uderzeń, w wyniku których wystające miejsca tych powierzchni ulegają stopniowemu niszczeniu, a same ziarna mielące ulegają zaokrągleniu i rozdrobnieniu na kawałki. Jeżeli jedna z powierzchni jest miękka, ziarna wciskają się w nią, pozostają w bezruchu, a na drugiej powierzchni powstają równoległe rysy; w pierwszym przypadku uzyskuje się matową powierzchnię pokrytą jednolitymi wżerami, w drugim tzw. „pociągnięcie” nadaje powierzchni połysk przechodzący w wypolerowanie, gdy obrys jest na tyle mały, że staje się niewidoczny dla oko. Tak więc, podczas szlifowania dwóch miedzianych płytek za pomocą szmergla, obie staną się matowe, a ten sam szmergiel, przyklejony do powierzchni papieru, nada połysk po potarciu o mosiężną powierzchnię.
Kruche, twarde szkło zużywa się bardziej niż miękka i elastyczna metalowa płytka, a proszek diamentowy może ścierać powierzchnię samego diamentu, a kawałki kwarcu można obrabiać na ostrzałce z piaskowca. Wgłębienia powstałe w wyniku ziaren szmergla są tym mniejsze, im drobniejsze są same ziarna; Dlatego szlifowanie może wytworzyć najbardziej precyzyjnie obrobione powierzchnie, tak jak ma to miejsce podczas szlifowania szkieł optycznych.
Rodzaje szlifowania
Szlifowanie płaszczyzn - obróbka płaszczyzn i łączenie powierzchni płaskich;
Szlifowanie taśmowe – obróbka płaszczyzn i łączenie powierzchni płaskich pasami „bezkońcowymi” (zamkniętymi w pierścieniu);
Szlifowanie cylindryczne - obróbka powierzchni cylindrycznych i stożkowych wałów i otworów.
Szlifowanie cylindryczne dzieli się na wewnętrzne (wytaczanie) i zewnętrzne. Z kolei wewnętrzne dzieli się na zwykłe i planetarne (zwykle - stosunek średnicy otworu części do średnicy przedmiotu obrabianego D = 0,9d, planetarne - D = (0,1...0,3)d);
Szlifowanie bezkłowe – obróbka przy wielkoseryjnej produkcji powierzchni zewnętrznych (wałów, bieżni łożyskowych itp.);
Szlifowanie gwintów;
Szlifowanie przekładni, szlifowanie.
Do głównych grup supertwarde materiały włączać diamenty, azotek boru, tlenek glinu (Glin 2 O 3 ) i azotek krzemu (Si 3 N 4 ) w postaci monokryształu lub w postaci proszku (ceramika mineralna).
Diament- sześcienna krystaliczna modyfikacja węgla, nierozpuszczalna w kwasach i zasadach. Wielkość diamentu mierzy się w karatach (jeden karat równa się 0,2 g). Istnieją naturalne techniczne (A) i polikrystaliczny syntetyczny (JAK) diamenty. Diamenty syntetyczne powstają w wyniku przekształcenia węgla w inną modyfikację dzięki znacznej zawartości grafitu w warunkach wysokich temperatur (~2500 0 C) i ciśnień (~1 000 000 MPa).
Gatunek syntetycznych diamentów polikrystalicznych ASB typ Bally produkowane są zgodnie z TU 2-037-19-76 (ASB-1, ASB-2, ..., ASB-5), diamenty polikrystaliczne ASPC typu carbonado - zgodnie z TU 2-037-96-73 (ASPK-1, ASPK-2, ASPK-3).
Oparte na materiałach sześcienny azotek boru (KNB) są podzielone na dwie grupy : materiały zawierające ponad 95% sześciennego azotku boru oraz materiały zawierające 75% sześciennego azotku boru z różnymi dodatkami (np. Al 2 O 3). Pierwsza grupa obejmuje Elbor – R(kompozyt 01), Geksanitować – R(kompozyt 10), Belbor (kompozyt 02), pomiń , PTNB . Do drugiej grupy zalicza się kompozyt 05 z ułamkiem masowym KNB 75% i Glin 2 O 3 25%.
Z ceramika mineralna Najczęściej stosowanymi materiałami narzędziowymi są następujące materiały: :
Ceramika tlenkowa (biała), który składa się z tlenku glinu (bezwodny naturalny tlenek glinu Al 2 O 3 około 99%) z niewielkimi dodatkami tlenku magnezu (MgO) lub innych pierwiastków. Wydawane są znaczki : TsM332, VSh-75 (TU 2-036-768-82 ); VO13 (TU 48-19-4204-2-79).
Tlenek glinu – korund. Stosuje się korund techniczny (naturalny) i syntetyczny. Korund syntetyczny jest szeroko stosowany elektrokorund (reprezentujący krystaliczny tlenek A1 2 O 3) gatunki 16A, 15A, 14A, 13A, 12A itd. I karborundy (reprezentujący związek chemiczny krzemu z węglem SiC) gatunki 55С, 54С, 53С, 52С, 64С, 63С, 62С.
Węglik tlenkowy(czarny) ceramika składa się z Al 2 O 3 (60 - 80%), ogniotrwałych węglików metali (TiC) i tlenków metali. Gatunki VOK60, VOK71 i V3 produkowane są zgodnie z GOST 25003-81.
Ceramika tlenkowo-azotkowa składa się z azotków krzemu (Si 3 N 4) i materiałów ogniotrwałych, w tym tlenku glinu i kilku innych składników. W tej grupie znajdują się marki : zapalenie kory - ONT-20(zgodnie z TU 2-R36-087-82) i silinit –R(wg TU 06-339-78).
Właściwości i zastosowanie materiałów narzędziowych
Materiały narzędziowe służą do produkcji narzędzi skrawających, pomiarowych, tłoczących i innych.
Materiały narzędziowe muszą mieć :
wysoka twardość, znacznie przewyższająca twardość obrabianego materiału;
wysoka odporność na zużycie niezbędna do utrzymania rozmiaru i kształtu krawędzi skrawającej podczas pracy;
wystarczająca wytrzymałość przy pewnej lepkości, aby zapobiec pękaniu narzędzia podczas pracy;
odporność na ciepło podczas przetwarzania ze zwiększoną prędkością.
Węgiel Stale narzędziowe przeznaczone są do produkcji narzędzi skrawających, które pracują bez znacznego nagrzewania krawędzi skrawającej (do 170...200°C) oraz matryc do odkształcania na zimno.
Stale o niższej zawartości węgla (U7, U7A), ponieważ są bardziej plastyczne, używa się ich do wyrobu instrumentów perkusyjnych : dłuta, przecinarki, przebijaki, młoty kowalskie, siekiery, tasaki; narzędzia hydrauliczne : przecinaki do drutu, szczypce, szczypce igłowe, śrubokręty, młotki; do matryc kuźniczych; drut igłowy; narzędzia do obróbki drewna : frezy, pogłębiacze, pogłębiacze itp.
Stać się U8, U8A, U8GA, U9, U9A - tworzywa sztuczne i stosowane do produkcji narzędzi pracujących w warunkach nie powodujących nagrzewania się krawędzi skrawającej; do obróbki drewna: frezy, pogłębiacze, pogłębiacze, siekiery, dłuta, dłuta, frezy wzdłużne i tarczowe; do rolek tocznych; dla kalibrów o prostych kształtach i niższych klasach dokładności itp.
Stać się U10,U10A - dobrze sprawdzają się bez dużych obciążeń udarowych i nagrzewania krawędzi skrawającej. Stosowane są do produkcji pił stolarskich, pił ręcznych, wierteł krętych, skrobaków, pilników, małych gwintowników ręcznych, matryc, rozwiertaków, tarników, pilników igłowych, matryc do tłoczenia na zimno, sprawdzianów gładkich i zszywek itp.
Ze stali U12, U12A produkować narzędzia o podwyższonej odporności na zużycie, pracujące przy umiarkowanych i znacznych naciskach bez nagrzewania krawędzi skrawającej : pilniki, żyletki, ostrza, ostre narzędzia chirurgiczne, skrobaki, przyrządy grawerskie, sprawdziany gładkie.
Stopowe Stale narzędziowe w porównaniu do stali węglowych mają wyższą twardość czerwoną (200...500 °C), odporność na zużycie i lepszą hartowność w porównaniu ze stalami węglowymi.
Stać się 9HS, HGS, HVG, HVSGF wykorzystywane do produkcji narzędzi skrawających (gwintowniki, matryce, rozwiertaki, przeciągacze, frezy itp.), a także narzędzi do tłoczenia do celów bardziej krytycznych niż te wykonane ze stali węglowych stosowanych do obróbki materiałów miękkich.
Stać się 8ХФ, 9ХФ, 11ХФ, 9ХФМ, 5ХНМ a inne służą do wytwarzania narzędzi do obróbki drewna (8HF), noże do cięcia metalu na zimno (9HF), piły budowlane, wykrojniki i stemple do gratowania na zimno, narzędzia chirurgiczne itp.
Wysoka prędkość stale charakteryzują się podwyższoną odpornością na zużycie i żaroodpornością (600...650°C), co pozwala na zastosowanie znacznie wyższych prędkości skrawania niż przy zastosowaniu narzędzi wykonanych ze stali węglowych i stopowych , wysoka wytrzymałość na zginanie i dobra szlifowalność w porównaniu do stopów węglików spiekanych.
Stale szybkotnące są jednym z głównych materiałów do produkcji narzędzi wieloostrzowych, które są trudne do szlifowania i naostrzenia.
Stać się P18 I R6M5 stosowany do produkcji wszelkiego rodzaju narzędzi skrawających do obróbki stali konstrukcyjnej.
Stać się R6M5F3 I R12F3 – do narzędzi wykańczających i półwykończeniowych (frezy, pogłębiacze, rozwiertaki, wiertła, przeciągacze, frezy itp.) do obróbki stali konstrukcyjnych i narzędziowych.
Stać się R9K5, R6M5K5, R18K5F2 – do narzędzi do obróbki zgrubnej i półwykończeniowej (frezy, frezy, gwintowniki, wiertła itp.) przeznaczonych do obróbki stali konstrukcyjnych.
Stać się P9 I 11R3AM3F2 – do narzędzi o prostych kształtach, do obróbki stali węglowych i niskostopowych.
Stać się R9M4K8 I R2AM9K5 – do wszystkich typów narzędzi stosowanych przy obróbce wysokowytrzymałych stali i stopów odpornych na korozję i żaroodporność.
Węglik spiekany mają wiele cennych właściwości : wysoka twardość połączona z dużą odpornością na zużycie podczas tarcia zarówno z materiałami metalowymi, jak i niemetalowymi; zwiększona odporność na ciepło (do 800...900°C).
Stopy twarde są szeroko stosowane w różnych gałęziach przemysłu : narzędzie tnące do obróbki ostrzy materiałów; wiertła do obróbki twardych skał; zęby nożyc i kombajnów w przemyśle węglowym; części robocze znaczków.
Zastąpienie narzędzi ze stali szybkotnącej narzędziami z węglików spiekanych zapewnia radykalny wzrost produktywności.
Grupa stopów TK bardziej twarde, żaroodporne i odporne na zużycie niż stopy grupy odpowiadającej zawartości kobaltu VC, ale jednocześnie bardziej kruche i mniej trwałe. Dlatego nie wytrzymują obciążeń udarowych, obróbki przerywanej i obróbki ze zmiennymi przekrojami ścinania.
T30K4– do toczenia wykańczającego o małym przekroju skrawania;
T15K6– do toczenia półzgrubnego podczas skrawania ciągłego , toczenie wykańczające z obróbką przerywaną , frezowanie półwykańczające i dokładne , wiercenie i wytaczanie wstępnie obrobionych otworów ;
T14K8– do toczenia zgrubnego, frezowania i pogłębiania w trakcie obróbki ciągłej, toczenia półwykańczającego i wykańczającego podczas obróbki przerywanej;
T5K10– do toczenia zgrubnego, frezowania, strugania wykańczającego.
Grupa stopów VC charakteryzuje się największą wytrzymałością, ale niską twardością.
Głównym przeznaczeniem twardych stopów wolframu (grupa VC) - obróbka żeliwa, metali nieżelaznych i ich stopów, materiałów niemetalicznych, stopów tytanu, niektórych gatunków stali i stopów odpornych na korozję, o wysokiej wytrzymałości i żaroodporności. Stopy z niewielką ilością kobaltu i drobnoziarnistych węglików wolframu (VK3, VK6-OM) stosowany do materiałów wykończeniowych i półwyrobowych. Stopy o średniej zawartości kobaltu (VK6, VK8)– do obróbki zgrubnej i półzgrubnej oraz o dużej zawartości kobaltu (VK10)– podczas zgrubnej obróbki materiałów. Typ stopu VK15 wytwarzać narzędzia skrawające do obróbki drewna.
Zastąpienie niektórych węglików tytanu węglikami tantalu w stopach grupy TTK zwiększa ich wytrzymałość (ciągliwość), odporność na pękanie podczas nagłych zmian temperatury i przerywanego cięcia. Pod względem wytrzymałości zajmują pozycję pośrednią pomiędzy stopami grup TK I VC.
Grupa stopów TTK stosowane są w obróbce zarówno stali, jak i żeliwa. Sprawdzą się w obróbce zgrubnej o dużym przekroju skrawania, podczas pracy z udarem (struganie, frezowanie) i wierceniu.
Nie zawiera wolframu stopy twarde Charakteryzują się dużą odpornością na zgorzelinę, przyczepnością i niskim współczynnikiem tarcia, ale mają obniżoną wytrzymałość i przewodność cieplną.
Bezwolframowe twarde stopy wykazują dobre wyniki w obróbce wykańczającej i półwykończeniowej metali i stali ciągliwych zamiast stopów T15K6, T14K8. Stopy te dają znaczący efekt przy wymianie stali narzędziowych na matryce, narzędzia pomiarowe: matryce, tłoczniki, formy, sprawdziany narzędzi pomiarowych itp. Z powodzeniem wykorzystywane są również jako narzędzia skrawające do obróbki metali nieżelaznych i stopów.
Twardość diamenty 6 razy większa twardość węglika wolframu i 8 razy większa twardość stali szybkotnącej. Przewodność cieplna diamentu jest kilkukrotnie większa od przewodności cieplnej innych materiałów narzędziowych, co kompensuje stosunkowo niską odporność cieplną - do 800°C (przy większym nagrzaniu diament ulega grafityzacji). Z dużych diamentów naturalnych i syntetycznych o wielkości do 120 mm wykonuje się: frezy, końcówki do pomiaru twardości metali, matryce, frezy do szkła, końcówki do wygładzania itp. Narzędzia diamentowe z diamentów naturalnych i syntetycznych można z powodzeniem wykorzystać do toczenia i wyroby wiertnicze z metali nieżelaznych i stopów, a także z materiałów niemetalowych i tworzyw sztucznych. Nie są zalecane do obróbki stali ze względu na silne oddziaływanie chemiczne.
Regularny azotek boru ( KNB ) ma twardość zbliżoną do diamentu, jest bardziej odporny na ciepło i chemicznie obojętny w porównaniu do diamentu, chociaż mniej przewodzi ciepło i ma wystarczającą udarność. Brak KNB powinowactwo chemiczne do żelaza pozwala na jego efektywne wykorzystanie do obróbki różnych stali trudnoskrawalnych, w tym nawęglanych i hartowanych, przy dużych prędkościach skrawania i małych grubościach skrawanych wiórów, co pozwala na zastąpienie szlifowania toczeniem lub przemiał.
Korund– minerał ustępujący jedynie diamentowi pod względem twardości, posiadający temperaturę topnienia 1750–2050°C . Najczystszymi przezroczystymi korundami są kamienie szlachetne - czerwony rubin i niebieski szafir. Korund techniczny wykorzystuje się jako materiał ścierny w produkcji optyki. Korundy syntetyczne – elektrokorundy – stosowane są do szlifowania stali i żeliwa, do ostrzenia narzędzi skrawających ze stali narzędziowych oraz do wykańczania narzędzi węglikowych.
Ceramika tlenkowa i tlenkowo-węglikowa Ma wystarczająco wysoką twardość i odporność na zużycie, ale jego wytrzymałość jest znacznie niższa niż twardych stopów, dlatego stosuje się go przede wszystkim do wykańczającej i częściowo półwykańczającej stali i żeliwa.
Ceramika tlenkowo-azotkowa Przeznaczone do obróbki stali hartowanych, żeliwa ciągliwego modyfikowanego i bielonego, stali ulepszanych cieplnie.
Diament syntetyczny (AS) i sześcienny azotek boru (CBN) (znaki towarowe: elboron, cubonit, borazon) należą do materiałów supertwardych (STM), których twardość przewyższa twardość tradycyjnych materiałów ściernych.
Diament- najtwardszy materiał znany nauce, składający się prawie wyłącznie z czystego węgla (C), którego atomy ułożone są w formie wąskiej, trójwymiarowej matrycy o dużej wytrzymałości. Diamenty reprezentowane są przez struktury mono- i makrokrystaliczne o doskonałej spójności.
W 1954 roku naukowcom z amerykańskiej firmy General Electrics udało się w warunkach laboratoryjnych zsyntetyzować diamenty z grafitu. W 1960 roku w ZSRR opanowano syntezę diamentów. Obecnie wielkość produkcji diamentów syntetycznych jest kilkakrotnie większa niż wielkość produkcji diamentów naturalnych. Większość diamentów syntetycznych ma strukturę monokrystaliczną. Możliwe kształty (morfologia) kryształów diamentu syntetycznego rozciągają się od kształtu sześciennego do kształtu ośmiościanu. Anizotropia twardości ścian diamentu wyznacza kierunki najmniej odporne na zużycie: w płaskiej siatce ośmiościanu - kierunki odpowiadające wysokościom ścian trójkątnych. ; w płaskiej siatce sześcianu - kierunki równoległe do boków ścian sześciennych. Największą twardość mają ściany sześcienne. Z kolei twardość ścian oktaedrycznych jest większa niż twardość rombowych dwunastościennych. W porównaniu do naturalnych, syntetyczne diamenty monokryształowe mają ostrzejsze krawędzie i mniejsze promienie zaokrąglenia wierzchołków krawędzi tnących, co wyjaśnia ich lepsze właściwości skrawające. Diament ma także najwyższy moduł sprężystości ze wszystkich znanych materiałów (moduł Younga E = 900 000 MPa). Przy najwyższej wytrzymałości na rozciąganie ze wszystkich znanych materiałów, wytrzymałość na rozciąganie diamentów podczas ściskania i zginania jest niewielka. Posiadając doskonałą spoistość, kryształy diamentu odrywają się, tworząc w zależności od wad strukturalnych pęknięcia równe, schodkowe lub muszlowe. Diamenty nie zwilżają się wodą, lecz przyklejają się do mieszanek tłuszczowych. Właściwość ta służy jako wskazówka przy wyborze rodzaju chłodziwa podczas szlifowania narzędziami diamentowymi (chłodziwa olejowe działają smarująco na ziarna diamentu, zmniejszając pracę tarcia). Diament charakteryzuje się wysoką przewodnością cieplną: jest ona od dwóch do pięciu razy większa niż w przypadku metali. Wysoka przewodność cieplna diamentu pozwala na szybkie usunięcie ciepła z powierzchni przedmiotu obrabianego. Niektóre metale, takie jak żelazo, częściowo rozpuszczają diament w temperaturach powyżej 800 0C, ograniczając jego zastosowanie.
Oprócz diamentów monokrystalicznych syntetyzowane są diamenty polikrystaliczne „carbonado” i „ballas”, które mają identyczną strukturę jak odpowiadające im diamenty naturalne. W wyniku spiekania diamentów syntetycznych w cylindryczne lub segmentowe granulki o ciemnej barwie powstają także diamenty polikrystaliczne typu „spiekanego”.
Regularny azotek boru jest sztucznym materiałem ściernym, głównie o składzie BN z gęstym sześciennym upakowaniem atomów boru i azotu w koordynacji tetraedrycznej.
Sześcienny azotek boru nie występuje naturalnie. Jego syntezę po raz pierwszy przeprowadziła w 1957 roku amerykańska firma General Electrics w wyniku eksperymentalnych poszukiwań nowych materiałów ściernych. Syntezę sześciennego azotku boru prowadzi się w taki sam sposób, jak produkcję syntetycznych diamentów.
Sześcienny azotek boru (CBN) jest wytwarzany z sześciokątnego azotku boru a-BN (gęstość 2,34 g/cm3) pod wysokim ciśnieniem i temperaturą. Przejściu sześciokątnego azotku boru do sześciennego towarzyszy 11,5-krotne zagęszczenie sieci krystalicznej. Główny składnik sześciennego azotku boru (b-BN) stanowi ponad 92%. Kolor kryształów waha się od białego i żółtego do ametystowego i czarnego.
Ze względu na bardziej złożoną strukturę atomową sześcienny azotek boru ma większą liczbę form krystalicznych. Z jednej strony możliwe kształty sześciennych kryształów azotku boru wahają się od kształtu sześciennego do kształtu ośmiościanu, jak diament; z drugiej strony możliwe kształty sześciennych kryształów azotku boru rozciągają się od kształtu ośmiościanu do kształtu czworościanu.
Materiały mielące CBN występują w dwóch rodzajach: z ziarnami o strukturze mono- i makrokrystalicznej (polikrystalicznej) oraz z mikrokrystalicznym składem granulometrycznym otrzymywanym w wyniku spiekania mikroproszków. sześciokątny lub wurcytopodobny azotek boru (BNB).
Jakie materiały są uważane za supertwarde? Jaki jest zakres ich zastosowania? Czy istnieją materiały twardsze od diamentu? Mówi o tym profesor, doktor krystalografii Artem Oganov.
Materiały supertwarde to materiały, które mają twardość powyżej 40 gigapaskali. Twardość jest właściwością tradycyjnie mierzoną poprzez zarysowanie. Jeśli jeden materiał zarysowuje drugi, uważa się, że ma on wyższą twardość. Jest to twardość względna; nie ma ścisłych cech ilościowych. Ścisłe ilościowe cechy twardości określa się za pomocą próby ciśnieniowej. Kiedy weźmiesz piramidę, zwykle wykonaną z diamentu, przyłóż pewną siłę i dociśnij piramidę do powierzchni badanego materiału, zmierz ciśnienie, zmierz powierzchnię wcięcia, zastosuj współczynnik korygujący, a ta wartość będzie twardość materiału. Ma wymiar ciśnienia, ponieważ jest siłą podzieloną przez powierzchnię, czyli gigapaskale (GPa).
40 GPa to twardość sześciennego polikrystalicznego azotku boru. Jest to klasyczny supertwardy materiał, który ma szerokie zastosowanie. Najtwardszym materiałem znanym dotychczas ludzkości jest diament. Od dawna trwają próby odkrycia materiału twardszego od diamentu, który trwa do dziś. Jak dotąd próby te nie zakończyły się sukcesem.
Dlaczego potrzebne są materiały supertwarde? Liczba materiałów supertwardych jest niewielka, obecnie znanych jest około dziesięciu, może piętnastu materiałów. Po pierwsze, materiały supertwarde można stosować do cięcia, polerowania, szlifowania i wiercenia. Do zadań związanych z budową obrabiarek, produkcją biżuterii, obróbką kamienia, górnictwem, wierceniem itd. wszystko to wymaga bardzo twardych materiałów.
Diament jest najtwardszym materiałem, ale nie jest materiałem najbardziej optymalnym. Faktem jest, że diament po pierwsze jest delikatny, a po drugie diament pali się w atmosferze tlenu. Wyobraź sobie wiertło, które nagrzewa się do wysokiej temperatury w atmosferze tlenu. Diament, będący węglem pierwiastkowym, będzie się palić. A poza tym diament nie przetnie stali. Dlaczego? Ponieważ węgiel reaguje z żelazem, tworząc węglik żelaza, co oznacza, że diament po prostu rozpuści się w stali w wystarczająco wysokiej temperaturze, dlatego należy poszukać innych materiałów. Ponadto diament jest oczywiście dość drogi; nawet diament syntetyczny nie jest wystarczająco tanim materiałem.
Co więcej, materiały supertwarde mogą nadal być przydatne w kamizelkach kuloodpornych i innych wojskowych urządzeniach ochronnych. W szczególności szeroko stosowany jest materiał taki jak węglik boru, który jest również bardzo twardy i dość lekki. Jest to zakres zastosowań materiałów supertwardych.
Wiadomo, że materiały supertwarde powstają w substancjach o silnych wiązaniach kowalencyjnych. Wiązanie jonowe zmniejsza twardość. Wiązanie metalu zmniejsza również twardość. Wiązania muszą być mocne, ukierunkowane, czyli kowalencyjne i możliwie krótkie. Gęstość substancji powinna być również tak wysoka, jak to możliwe, gęstość w sensie liczby atomów na jednostkę objętości. I jeśli to możliwe, symetria substancji powinna być również bardzo wysoka, aby substancja była równie silna w tym kierunku, w tym i w tym. W przeciwnym razie historia będzie taka sama jak w graficie, gdzie wiązania są bardzo mocne, ale tylko w dwóch kierunkach, a w trzecim kierunku wiązania między warstwami są wyjątkowo słabe, w efekcie substancja jest również miękka.
Wiele instytutów, wiele laboratoriów na całym świecie zajmuje się syntezą i rozwojem materiałów supertwardych. W szczególności są to Instytut Fizyki Wysokich Ciśnień w obwodzie moskiewskim, Instytut Supertwardych i Nowych Materiałów Węglowych w obwodzie moskiewskim, Instytut Materiałów Supertwardych w Kijowie oraz szereg laboratoriów na Zachodzie. Aktywny rozwój w tej dziedzinie rozpoczął się, jak sądzę, w latach 50. XX wieku, kiedy w Szwecji i Ameryce po raz pierwszy wyprodukowano sztuczne diamenty. Początkowo odkrycia te były tajne, ale wkrótce synteza sztucznych diamentów została rozpoczęta także w Związku Radzieckim, właśnie dzięki pracom naukowców z Instytutu Wysokich Ciśnień i Instytutu Materiałów Supertwardych.
Podejmowano różne próby stworzenia materiałów twardszych niż diament. Pierwsza próba opierała się na fulerenach. - są to cząsteczki przypominające piłkę nożną, cząsteczki puste w środku, okrągłe lub nieco wydłużone. Wiązania między tymi cząsteczkami są bardzo słabe. Oznacza to, że jest to kryształ molekularny składający się ze zdrowych cząsteczek. Ale wiązania między cząsteczkami są słabe, van der Waals. Jeśli taki kryształ zostanie ściśnięty, wówczas zaczną tworzyć się wiązania pomiędzy cząsteczkami, pomiędzy tymi kulkami, a struktura zamieni się w trójwymiarowo połączoną kowalencyjną, bardzo twardą strukturę. Materiał ten został nazwany tisnumite na cześć Instytutu Technologicznego Supertwardych i Nowych Materiałów Węglowych. Zakładano, że materiał ten jest twardszy od diamentu, jednak dalsze badania wykazały, że najprawdopodobniej tak nie było.
Pojawiły się propozycje i dość ożywiona dyskusja, że azotki węgla mogą być twardsze od diamentu, jednak pomimo aktywnych dyskusji i aktywnych badań, taki materiał nie został jeszcze zaprezentowany światu.
Pojawiła się dość zabawna praca chińskich badaczy, w której na podstawie obliczeń teoretycznych zasugerowali, że inna modyfikacja węgla jest pod wieloma względami podobna do diamentu, ale nieco się od niej różni i nazywa się lonsdaleit. Według tej pracy lonsdaleit jest twardszy niż diament. Lonsdaleit jest interesującym materiałem; cienkie blaszki tego materiału znaleziono w diamentach sprasowanych udarowo. Minerał ten został nazwany na cześć słynnej kobiety Kathleen Lonsdale, wielkiej brytyjskiej krystalografki żyjącej w latach 50. – 70. XX wieku. Miała niezwykle ciekawą biografię, spędziła nawet czas w więzieniu, gdy odmówiła gaszenia pożarów podczas II wojny światowej. Z religii była kwakierką i kwakrzym nie wolno było podejmować żadnej działalności związanej z wojną, nawet gasić pożary. I w tym celu wsadzili ją do wozu ryżowego. Niemniej jednak wszystko było z nią w porządku, była prezesem Międzynarodowej Unii Krystalografii, a na jej cześć nazwano ten minerał.
Lonsdaleit, sądząc po wszystkich dostępnych danych eksperymentalnych i teoretycznych, jest nadal bardziej miękki niż diament. Jeśli spojrzysz na prace tych chińskich badaczy, zobaczysz, że nawet według ich obliczeń lonsdaleit jest bardziej miękki niż diament. Ale w jakiś sposób wyciągnięto wniosek wbrew ich własnym wynikom.
Okazuje się zatem, że nie ma realnego kandydata, który mógłby zastąpić diament w roli najtwardszej substancji. Niemniej jednak warto zbadać tę kwestię. Mimo to wiele laboratoriów wciąż próbuje stworzyć taki materiał. Korzystając z naszej metody przewidywania struktur krystalicznych, postanowiliśmy zadać to pytanie. A problem można sformułować następująco: nie szukasz substancji o maksymalnej stabilności, ale substancji o maksymalnej twardości. Podajesz zakres składów chemicznych, na przykład od czystego węgla do czystego azotu i wszystko pomiędzy, wszystkie możliwe azotki węgla, są uwzględniane w twoich obliczeniach i ewolucyjnie próbujesz znaleźć coraz trudniejsze kompozycje i struktury.
Najtwardszą substancją w tym układzie jest ten sam diament, a dodanie azotu do węgla niczego w tym układzie nie poprawia.
Tym samym można obalić hipotezę o azotkach węgla jako substancjach twardszych od diamentu.
Próbowaliśmy wszystkiego, co sugerowano w literaturze, różnych form węgla itd. – we wszystkich przypadkach diament zawsze wygrywał. Wygląda więc na to, że diamentu nie da się usunąć z tego cokołu. Możliwe jest jednak wynalezienie nowych materiałów, które będą lepsze od diamentu pod wieloma innymi względami, na przykład pod względem odporności na pękanie lub odporności chemicznej.
Na przykład pierwiastkowy bor. Odkryliśmy strukturę, nową modyfikację boru. Opublikowaliśmy ten artykuł w 2009 roku i wywołał on ogromny odzew. Strukturę uzyskuje się poprzez przyłożenie niewielkiego nacisku na zwykły bor i podgrzanie go do wysokich temperatur. Nazwaliśmy tę formę gamma-borem i okazało się, że zawiera ona częściowe jonowe wiązanie chemiczne. Tak naprawdę jest to coś, co nieznacznie obniży twardość, jednak ze względu na dużą gęstość modyfikacja ta i tak okazuje się najtwardszą znaną modyfikacją boru, jej twardość wynosi około 50 GPa. Presje na syntezę są niewielkie, dlatego w zasadzie można nawet myśleć o jej syntezie w dość dużych objętościach.
Przewidzieliśmy szereg innych faz supertwardych, takich jak fazy w układzie wolfram-bor, chrom-bor i tak dalej. Wszystkie te fazy są supertwarde, ale ich twardość wciąż mieści się w dolnej granicy tego zakresu. Bliżej im jest do 40 GPa niż do 90–100 GPa, co odpowiada twardości diamentu.
Jednak poszukiwania trwają, nie poddajemy się rozpaczy i jest całkiem możliwe, że my lub nasi koledzy pracujący nad tym tematem na całym świecie będziemy w stanie wynaleźć materiał, który będzie można syntetyzować pod niskim ciśnieniem i który będzie zbliżony do diamentu twardość. My i inni koledzy zrobiliśmy już coś w tym obszarze. Ale jak zastosować to technologicznie, nie jest jeszcze całkowicie jasne.
Opowiem Wam o nowej formie węgla, która została faktycznie wyprodukowana eksperymentalnie w 1963 roku przez amerykańskich badaczy. Eksperyment był koncepcyjnie dość prosty: pobrano węgiel w postaci grafitu i sprasowano go w temperaturze pokojowej. Faktem jest, że w ten sposób nie można uzyskać diamentu; diament wymaga silnego nagrzania. Zamiast diamentu w ich eksperymentach utworzyła się przezroczysta, supertwarda faza niemetaliczna, ale mimo to nie był to diament. Nie było to w żaden sposób zgodne z charakterystyką żadnej ze znanych form węgla. O co chodzi, co to za konstrukcja?
Całkiem przypadkowo, badając różne struktury węgla, natknęliśmy się na jedną strukturę, która pod względem stabilności tylko nieznacznie ustępowała diamentowi. Dopiero trzy lata po tym, jak zobaczyliśmy tę strukturę, przyjrzeliśmy się jej, a nawet opublikowaliśmy gdzieś pomiędzy wierszami, dotarło do nas, że fajnie byłoby porównać właściwości tej struktury z tym, co publikowali wszyscy ci badacze od 1963 roku i prawda aż do bardzo ostatnich lat. I okazało się, że jest to zupełny przypadek. Byliśmy szczęśliwi, szybko opublikowaliśmy artykuł w jednym z najbardziej prestiżowych magazynów, Listy przeglądu fizycznego, a rok później w tym samym czasopiśmie ukazał się artykuł amerykańskich i japońskich badaczy, którzy odkryli, że zupełnie inna struktura węgla opisuje również te same dane eksperymentalne. Problem polega na tym, że dane eksperymentalne miały raczej słabą rozdzielczość. Kto więc ma rację?
Wkrótce szwajcarscy i chińscy badacze zaproponowali szereg modyfikacji. Pod koniec jeden z chińskich badaczy opublikował około czterdziestu struktur węglowych, z których większość opisuje również te same dane eksperymentalne. Obiecał mi, że jeśli nie będzie zbyt leniwy, zaproponuje jeszcze około stu konstrukcji. Jaka jest zatem właściwa struktura?
Aby tego dokonać, musieliśmy zbadać kinetykę przemiany grafitu w różne struktury węglowe i okazało się, że mieliśmy dużo szczęścia. Okazało się, że nasza struktura jest najkorzystniejsza z punktu widzenia kinetyki transformacji.
Miesiąc po opublikowaniu naszego artykułu ukazała się praca eksperymentalna, w której eksperymentatorzy przeprowadzili najdokładniejszy eksperyment z danymi o znacznie lepszej rozdzielczości niż dotychczas i rzeczywiście okazało się, że spośród kilkudziesięciu opublikowanych struktur tylko jedna konstrukcja wyjaśnia dane eksperymentalne - to wciąż nasza struktura. Nazwaliśmy ten nowy materiał M-węglem, ponieważ jego symetria jest jednoskośna, począwszy od pierwszej litery M.
Materiał ten jest tylko nieznacznie gorszy od diamentu pod względem twardości, ale nadal nie jest jasne, czy istnieje jakaś właściwość, w której jest lepszy od diamentu.
Do tej pory jest to, można powiedzieć, „rzecz sama w sobie”. Kontynuujemy poszukiwania i mamy nadzieję, że uda nam się wynaleźć materiał, który choć niewiele gorszy od diamentu pod względem twardości, znacznie go przewyższy we wszystkich innych cechach.
Jednym ze sposobów poprawy właściwości mechanicznych substancji jest ich nanostruktura. W szczególności twardość tego samego diamentu można zwiększyć tworząc nanokompozyty diamentowe lub nanopolikryształy diamentu. W takich przypadkach twardość można zwiększyć nawet 2-krotnie. I tego dokonali japońscy badacze, i teraz można zobaczyć produkty, które wytwarzają, dość duże, rzędu centymetra sześciennego, nanopolikryształy diamentu. Główny problem z tymi nanopolikryształami polega na tym, że są tak twarde, że prawie niemożliwe jest ich wypolerowanie, a polerowanie ich zajmuje całe laboratorium tygodniami.
W ten sposób można zarówno zmienić skład chemiczny, strukturę substancji w celu poprawy jej twardości i innych właściwości, jak i zmienić wymiar.